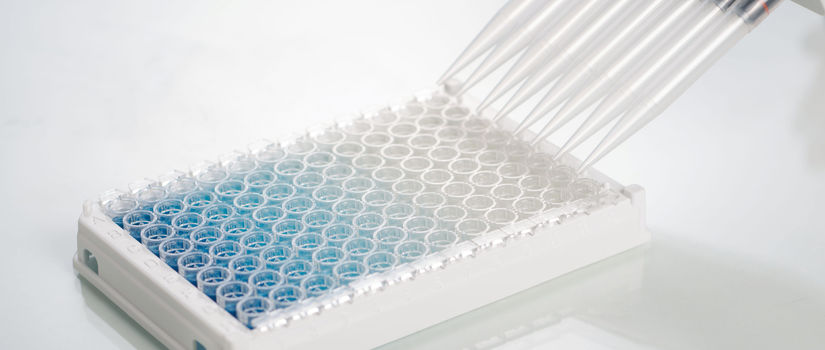
Vaccines are biological products intended to deliver antigens with the scope to induce an immune response and immune memory against a particular disease. Vaccines can be prophylactic or therapeutic and generate immunity by humoral or cellular response.
Manufacturing of vaccines is a very challenging activity, because the outcome of this process may vary due to many factors, specifically the mutability of the microorganism or the biological antigen over the time, the starting materials, the environment, the purification process or the adjuvants used. Nevertheless, the profile of all lots for marketing use should be consistent during the time and effective quality control tests should be implemented by pharmaceutical companies.
Historically, quality control of vaccines has been executed by testing the potency of the final product in animals of different species. Nowadays companies are facing new vaccine developments and update of existing ones by means of in vitro biological assays for the estimation of the potency.
Method Validation
Usually live vaccines require cell-based assays, that use a specified cell system to demonstrate a measureable biological response. On the contrary subunit, toxoid, conjugate and allergy vaccines can be reliably monitored with immunoassays.
A major handicap is the validation of the assay test that according to ICH Q2 (R1) has to be able to quantify the active moiety in samples. The GMP requirements for the validation assay are accuracy, precision, repeatability, intermediate precision, specificity, limit of detection, linearity and range.
Nowadays, human and veterinary pharmaceutical companies are developing quality control potency assays for new vaccines almost exclusively using in vitro testing. For existing products, although replacement of in vivo tests for batch release of existing vaccines may be difficult, there are a lot of advantages including improvement in method reproducibility, simplification of method transfer between different labs, saving of experimental animals, improvement of manufacturing lead times, and cost reduction.
If you want to learn more about our services in Method Development and Validation, click here.